Building for climate
The construction industry accounts for more than a third of the world’s carbon emissions. The sector must urgently ramp up new methods to slash CO2 from the construction lifecycle if we’re to achieve net zero
Climate — Global
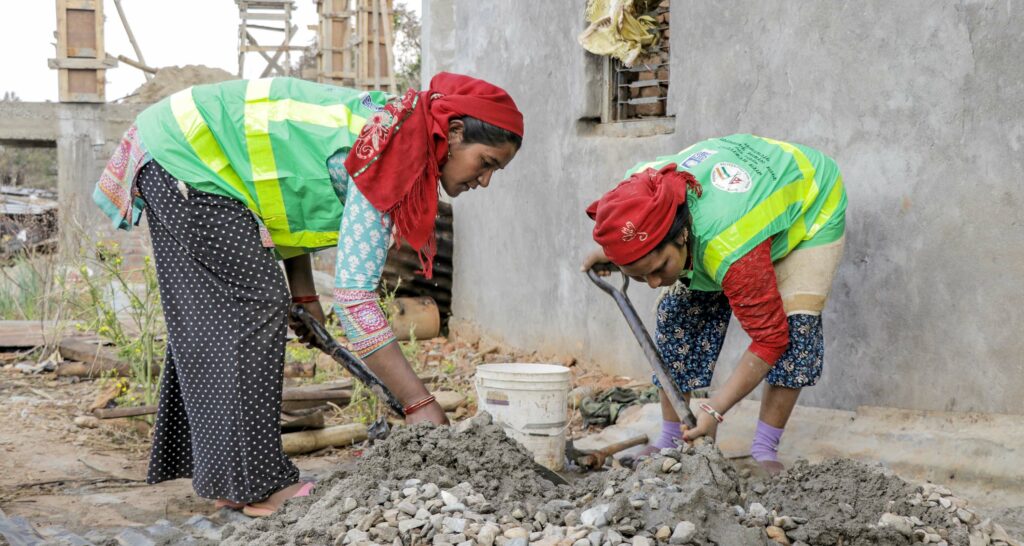
The world is facing a dilemma between climate, economic, and social goals. Around one billion people live in slum conditions, many without access to decent sanitation. Continued construction is a key element to achieving most of the Sustainable Development Goals. The demand for affordable construction materials will therefore increase – especially in the Global South, which is experiencing high population growth and fast urbanization.
The critical question is: how can we meet this demand without negatively impacting climate change and other environmental goals?
Concrete and other materials based on cement are by far and away the most widely used construction materials, due to their ease of use, flexibility, and low cost. There is a widespread misconception that these materials have a high environmental impact, as they are responsible for around 7% to 8% of annual CO2 emissions. However, this is simply due to the vast amounts of cement-based materials we use – around 30 billion tonnes per year. On a per kg basis, the emissions from cement-based materials are among the lowest of all materials.
In addition, cement-based materials cannot be replaced in any meaningful way by other materials, purely from a resource perspective. It has been estimated that to replace just one quarter of concrete with wood we would have to plant new sustainable forest one and a half times the area of India. Even if this could be done it would take 30 years or so to produce timber.
There is no miracle, “new” cement out there that can avoid the associated CO2 emissions. Nevertheless, there are many ways in which the environmental impact of construction can be reduced.
Three ways to minimize emissions
Minimizing CO2 requires working through the whole value chain of construction. For example, for cement-based materials, it must start with the production of “clinker” – the product of a cement kiln, which when ground provides the basis for more than 99% of cement used today. We must reduce to the minimum necessary:
- the amount of clinker in the cement to achieve the required performance
- the amount of cement in the concrete
- the amount of concrete needed for a building
If all these steps could be brought together it is estimated that, even with known technologies, overall CO2 emissions due to cement-based materials could be reduced by about 70% to 80%.
How do we achieve this? At the clinker level, the process is already well optimized. Areas of potential progress are increasing the use of alternative fuels and further heat recovery. Alternative fuels are various kinds of non-recyclable waste, such as car tires. Their use is highly effective to avoid landfill and to safely breakdown materials such as plastics. Many cement plants, particularly in Europe, already operate with levels of alternative fuels above 90%, but the level of substitution in most of the Global South is only a few percent. Increasing this is largely a question of waste management – making large enough disincentives to avoid waste being sent to landfill or simply dumped. Improving the amount of waste into fuel would make a significant contribution to reducing fossil fuel demand and to better waste disposal.
At the level of cement, using other materials to partially substitute clinker is a strategy that has been followed for several decades. Two of the most used substitutes are:
- “fly ash,” a residue of burning coal for electricity
- ground-granulated blast furnace slag (GGBS or “slag”), a by-product of producing iron from iron ore
Today the availability of these materials is limited to around 15% of consumed cement. Both materials come from highly carbon-intensive processes that will (hopefully) disappear in coming decades.
The other, most widely used, substitute material – fine limestone – is available in effectively unlimited amounts, but cannot be used at high substitution levels without a loss of properties. Due to these limitations the average level of substitution worldwide has stagnated at around 20% for the past 10 to 15 years. Fortunately, the development of limestone calcined clay cement (LC3) technology in our laboratory at EPFL, and with partners in India and Cuba, provides a new way forward.
LC3 uses a coupled substitution of limestone together with calcined clay to produce cement with excellent properties at high levels of substitution. Calcined clay is clay which has been heated to around 800°C. This disrupts the crystal structure and produces a very reactive clinker substitute. Similar mechanical properties to classic “ordinary Portland cement” (which has around 90% clinker) can be obtained with only 50% clinker, 30% calcined clay, 15% limestone, and 5% gypsum. Even though some energy is needed for the clay calcination, this represents a saving of around 40% in CO2 emissions.
Clay suitable for calcination is extremely abundant worldwide, especially in the Global South where the biggest demand for buildings will be in the coming decades. Currently there are four plants producing LC3, with at least 20 more expected within the next two years. On a global scale, increasing the substitution level has the potential to save 400 to 800 million tonnes of CO2 per year compared with business as usual.
Large savings are also possible at the next level, concrete. Simply choosing a good aggregate size or using superplasticisers can lead to CO2 reductions of around 30% to 50%. On a global level, such savings would be helped by wider use of ready-mix concrete (where good control of the concrete recipe is easier) rather than on-site mixing. Even in more developed countries where ready-mix comprises the vast majority of the market, large savings in cement (and CO2) can be achieved by modernizing concrete recipes, using modern admixtures, and getting rid of outdated concepts like minimum cement content.
The final level of optimization is the amount of material in a building. Savings here can be as simple as sticking to the codes and not systematically adding another 10% to 20% of materials “just to be on the safe side.” Smart use of codes and lean design can often lead to even higher savings – for example, shorter spacings between columns, or avoiding deep basements and cantilevers. Building height also matters: a single 50-storey skyscraper requires twice as much material for vertical elements than two 25-storey buildings.
A coordinated approach
An increasing number of actors in the industry are looking to lower emissions, but are challenged by the fact that the sector involves a large number of uncoordinated, competing businesses and has small profit margins. To achieve the large potential for CO2 savings, different parts of the construction industry must work together better. Investors, owners, operators, planners, developers, architects, and designers all influence the construction decision-making process. They are therefore all responsible for optimizing construction sustainability.
There is a strong need to establish an organisational framework, including the various stakeholders, to ensure that adequate incentives to act sustainably are identified and implemented throughout the value chain. Global benchmarking of construction practices, materials, and their carbon intensities can contribute to identify opportunities to reduce emissions.
One action that stakeholders can take now is to join the Global Consensus on Sustainability in the Built Environment – GLOBE. It aims to “direct the attention of the global community… to the critical importance of the built environment for sustainable development.” I encourage all those active in construction to join this consensus and work together to realize climate-friendly buildings and construction.